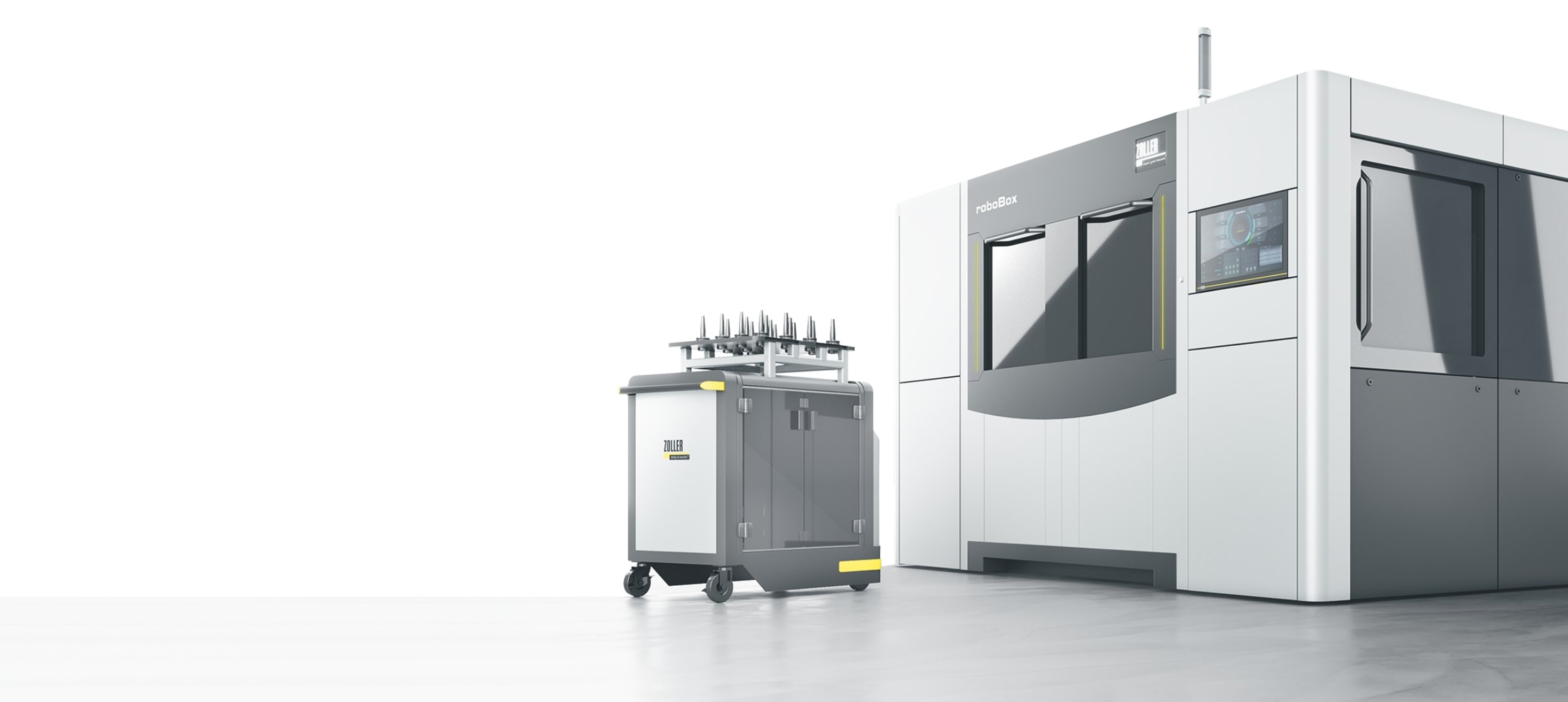
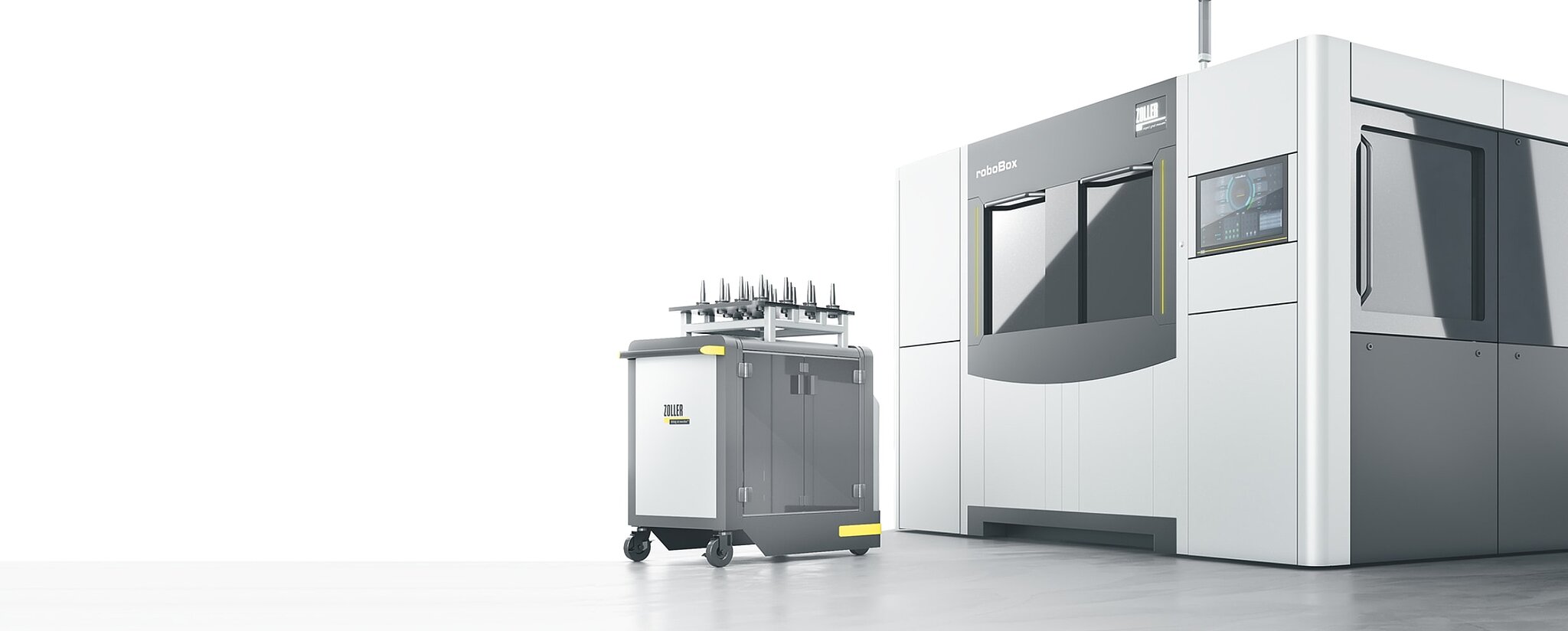
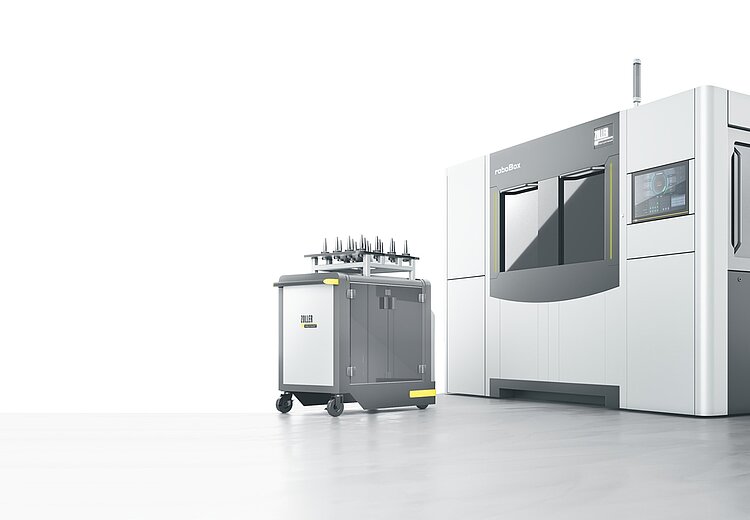
Featured
Technology
at the IMTS!
We will customize a solution
that optimizes and fits your
desired process for your shop!
Premier of the »powerShrink 400/600«
The New Shrink-clamping system solution from ZOLLER!
Clamping and unclamping tools in record time and saving energy and conserving tool holders: You get all these benefits with the new inductive »powerShrink« heat shrink system. Our product development team factored in maximum energy efficiency as well as a fast and reliable shrinking process which is very important for ZOLLER customers – allowing more profitability and efficiency in their shops! Click on the link below to see Michael Colyer, Territory Manager and job shop owner gave an impressive introduction to this amazing new solution for heat shrinking and clamping your tools!
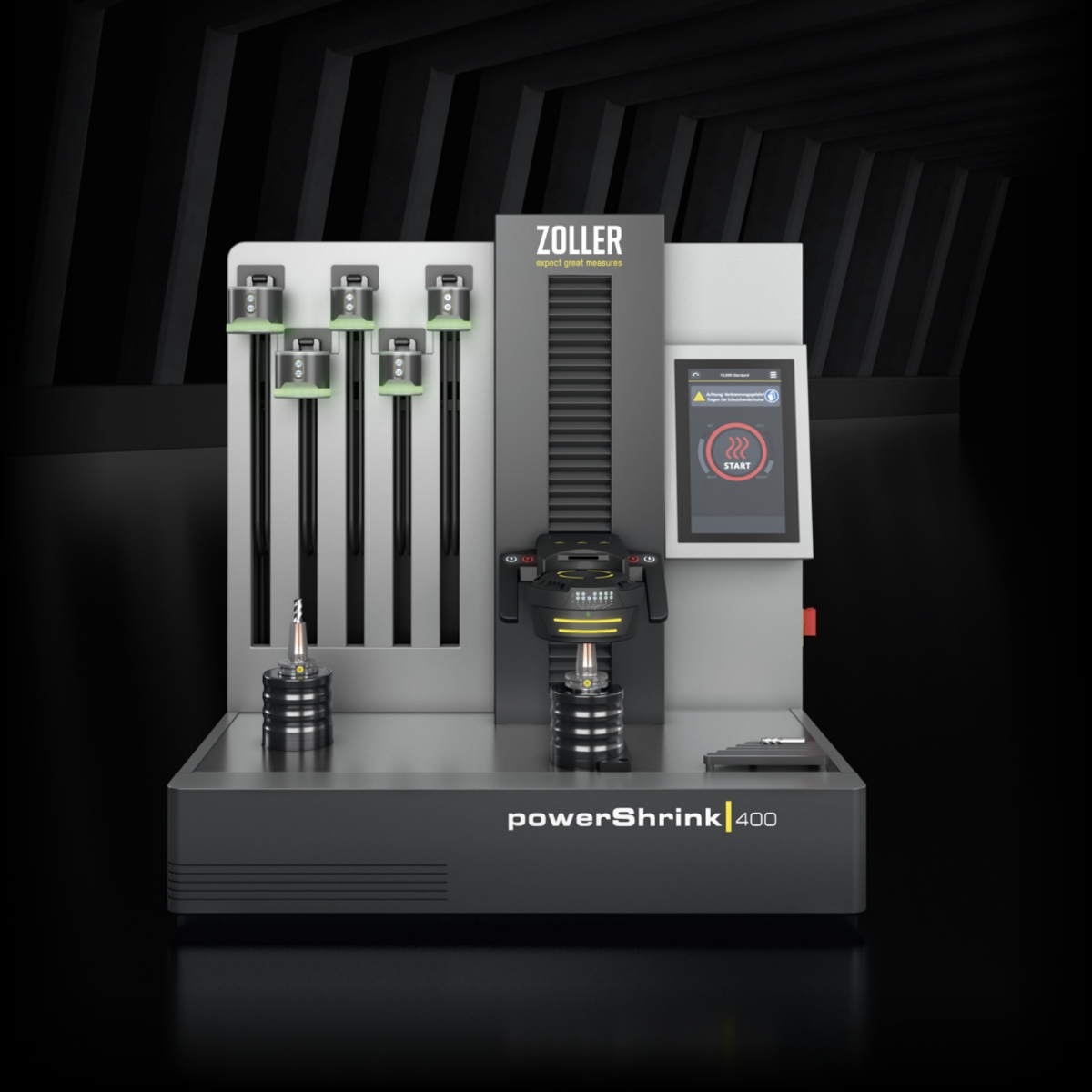
Premier of the »powerShrink 400/600«
The New Shrink-clamping system solution from ZOLLER!
Clamping and unclamping tools in record time and saving energy and conserving tool holders: You get all these benefits with the new inductive »powerShrink« heat shrink system. Our product development team factored in maximum energy efficiency as well as a fast and reliable shrinking process which is very important for ZOLLER customers – allowing more profitability and efficiency in their shops! Click on the link below to see Michael Colyer, Territory Manager and job shop owner gave an impressive introduction to this amazing new solution for heat shrinking and clamping your tools!
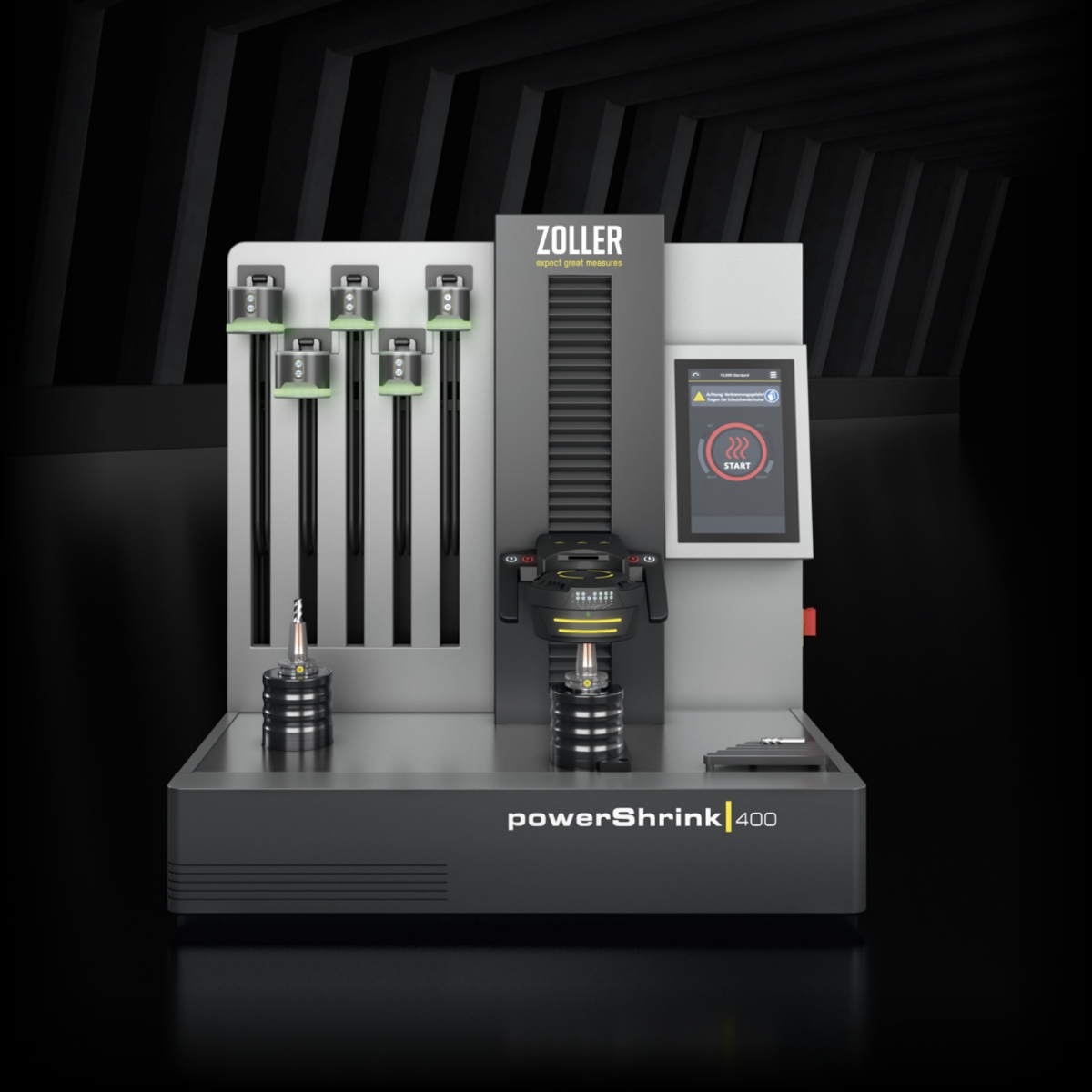
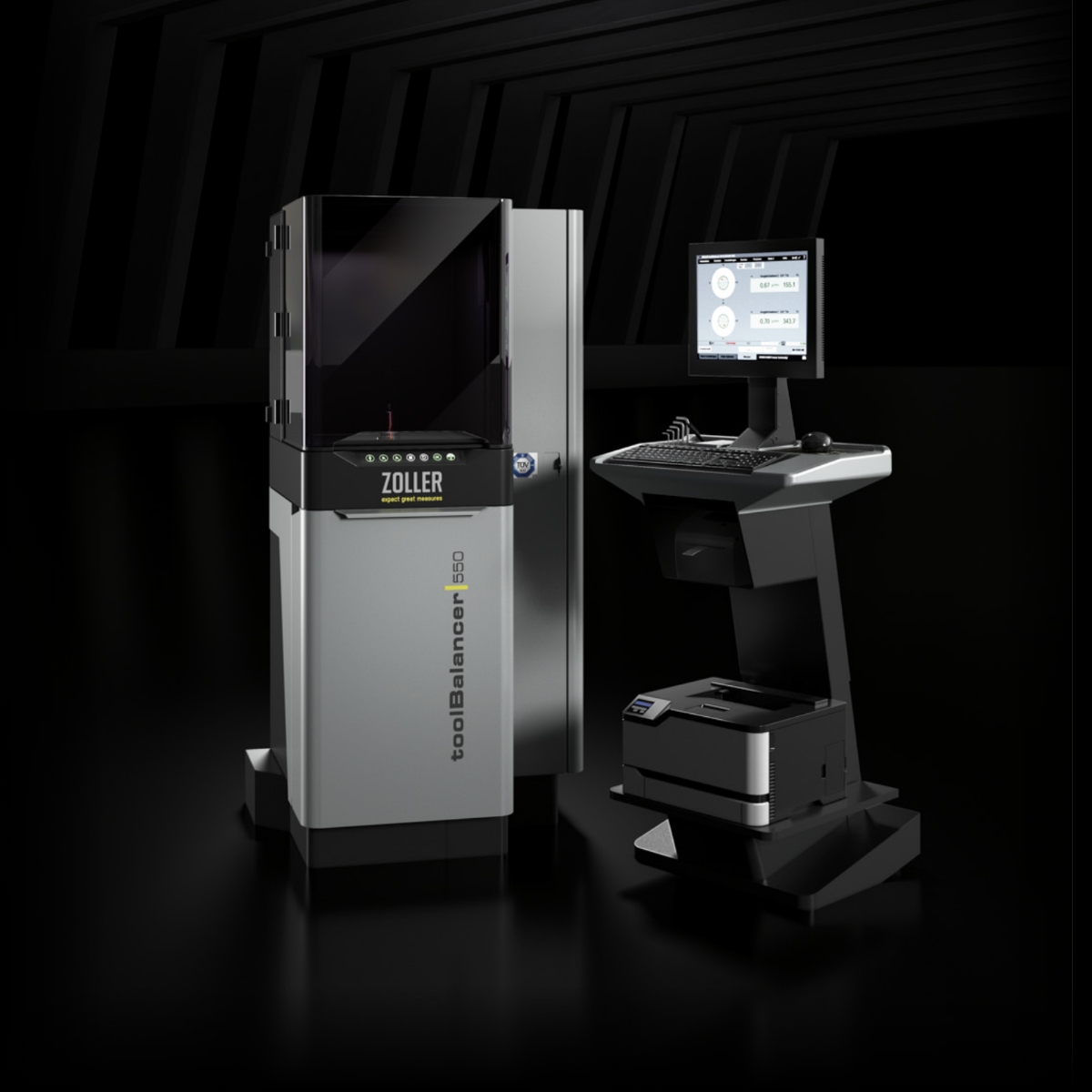
North American Premier of the »toolBalancer 550/750«
The New Balancing System Solution from ZOLLER!
The gamechanging »toolBalancer« enables you to increase your process reliability and the quality of your components, reduce machine maintenance costs and prevent machine failures. How does it work? It’s simple: Highly-precisely balanced tools allow you to achieve longer tool life, higher spindle running time and better surface quality of your components. Check out the introduction video from ZOLLER Inc. Michael Colyer from the show!
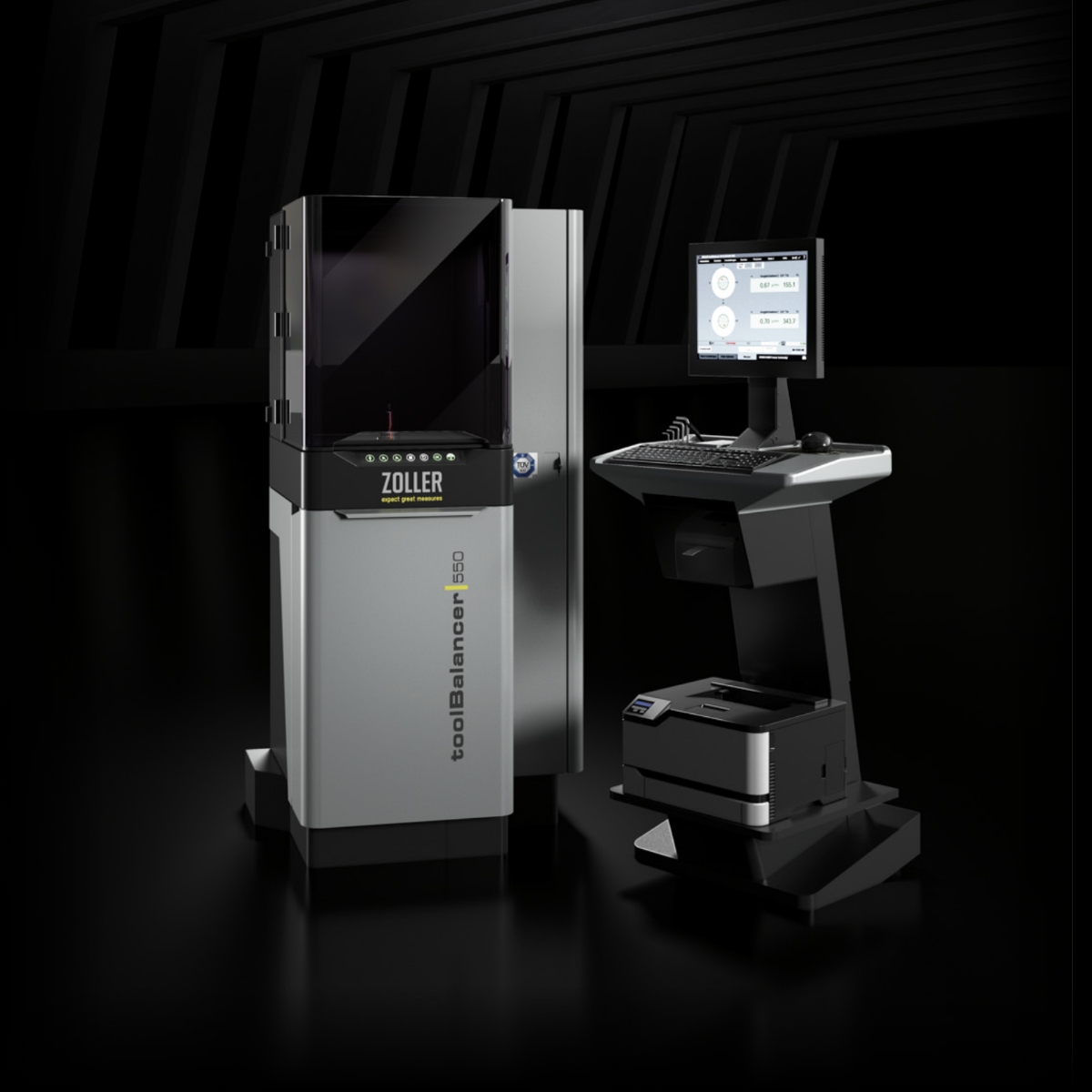
North American Premier of the »toolBalancer 550/750«
The New Balancing System Solution from ZOLLER!
The gamechanging »toolBalancer« enables you to increase your process reliability and the quality of your components, reduce machine maintenance costs and prevent machine failures. How does it work? It’s simple: Highly-precisely balanced tools allow you to achieve longer tool life, higher spindle running time and better surface quality of your components. Check out the introduction video from ZOLLER Inc. Michael Colyer from the show!
Automation Solution- Premier in North America!
»roboBox«
ZOLLER was super excited to make the premier of the »roboBox« ,the central systems component gamechanger for your digitized, automated Industry 4.0 production process.Visitors to the ZOLLER booth experienced first hand this revolutionary Automated Modular Assembly and Measurement System for Cutting Tools. The responce to this system solution that automatically assembles shrink fit holders and cutting tools together was overwhelming! Everyone was also amazed at the ease of which one can fully integrate automatic tool logistics and delivery into your production process!
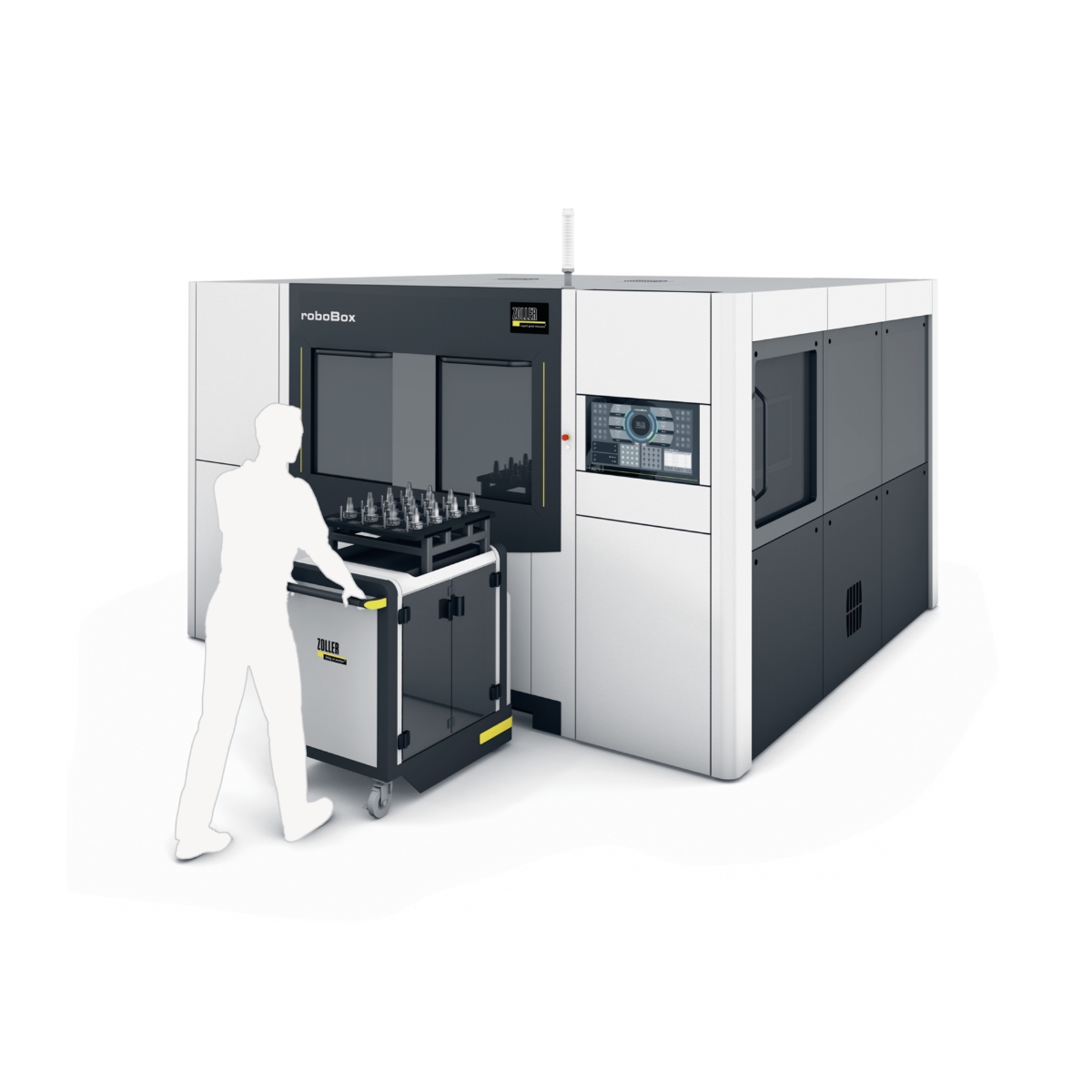
Automation Solution- Premier in North America!
»roboBox«
ZOLLER was super excited to make the premier of the »roboBox« ,the central systems component gamechanger for your digitized, automated Industry 4.0 production process.Visitors to the ZOLLER booth experienced first hand this revolutionary Automated Modular Assembly and Measurement System for Cutting Tools. The responce to this system solution that automatically assembles shrink fit holders and cutting tools together was overwhelming! Everyone was also amazed at the ease of which one can fully integrate automatic tool logistics and delivery into your production process!
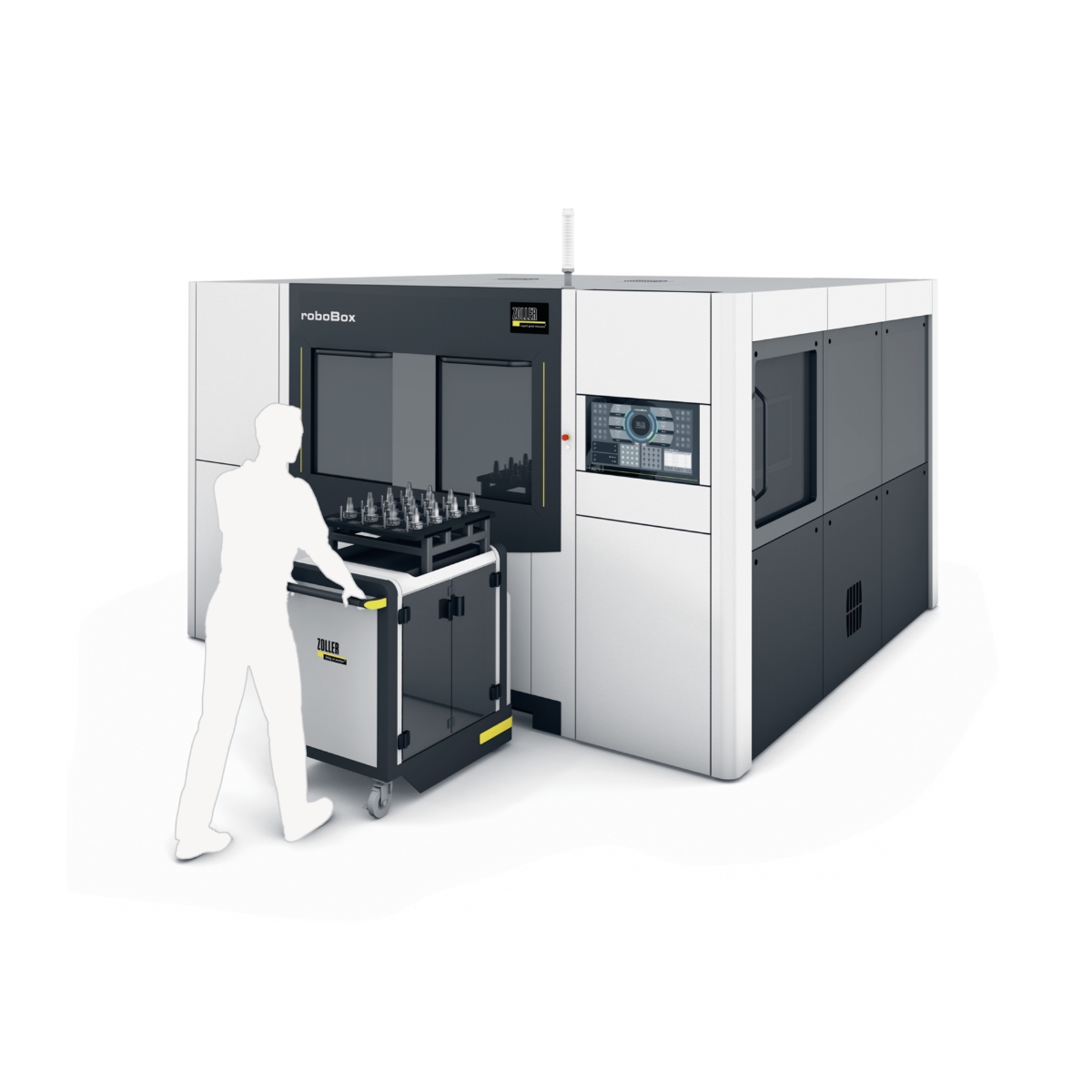
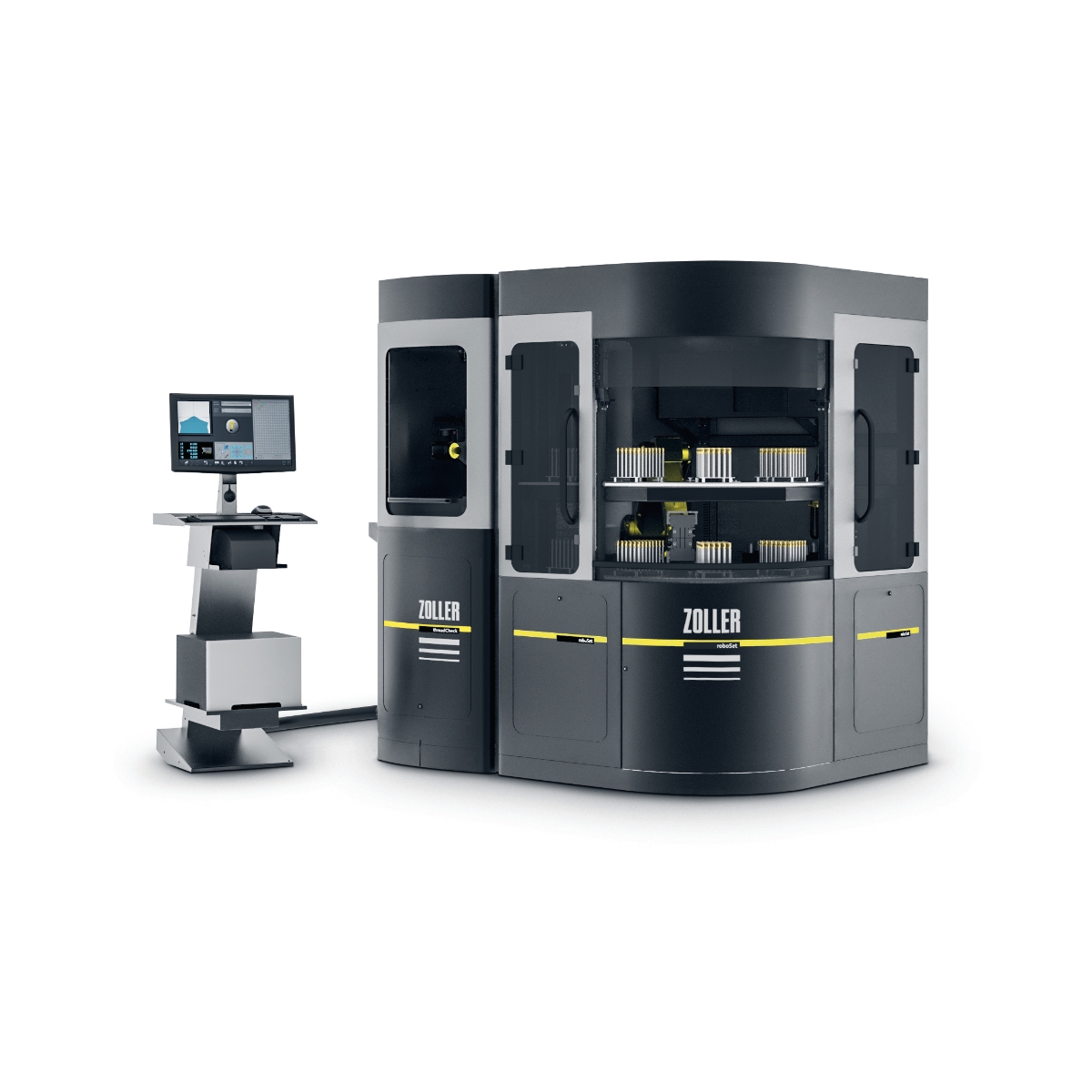
Automation Solution- Lights out Cutting Tool Inspection!
»roboSet 2«
At Booth W-432018 at the IMTS, see the industry gamechanger for 24/7 light out cutting tool inspection solution for efficient quality control! Your production throughput can be maximised with the fully automated loading station that allows a ZOLLER »genius« machine to operate with total accuracy around the clock. Predefined program selection within pilot 3.4 software caters for the recording of more than 50 measurement parameters with micron precision without any operator intervention. Once the checking procedure is complete, faulty tools are automatically separated from the correct ones.
It’s the perfect solution for efficient quality control at high tool volumes. Schedule your one on one meeting and demo with our experts at the IMTS at Booth W-432018 to get more information on how the »roboSet 2« can become a gamechanger for your facility!
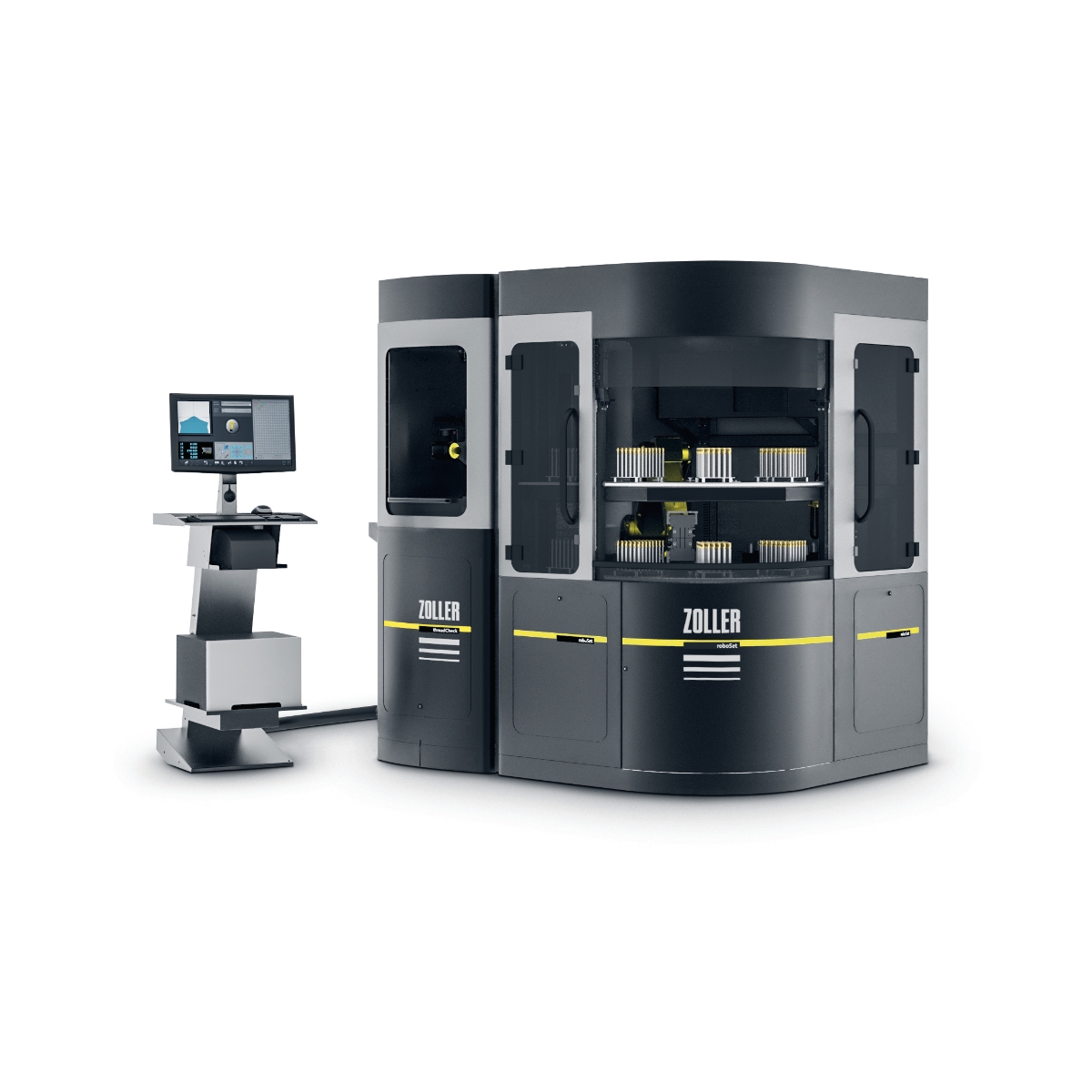
Automation Solution- Lights out Cutting Tool Inspection!
»roboSet 2«
At Booth W-432018 at the IMTS, see the industry gamechanger for 24/7 light out cutting tool inspection solution for efficient quality control! Your production throughput can be maximised with the fully automated loading station that allows a ZOLLER »genius« machine to operate with total accuracy around the clock. Predefined program selection within pilot 3.4 software caters for the recording of more than 50 measurement parameters with micron precision without any operator intervention. Once the checking procedure is complete, faulty tools are automatically separated from the correct ones.
It’s the perfect solution for efficient quality control at high tool volumes. Schedule your one on one meeting and demo with our experts at the IMTS at Booth W-432018 to get more information on how the »roboSet 2« can become a gamechanger for your facility!
Inspection Solution »genius«
The best selling »genius« is a universal measuring machine and is the perfect solution for the measurement and inspection of your cutting tools quickly, simply and precisely. It can easily handle everything from the quick testing of individual criteria to the fully automatic and operator-independent measurement of more than 100 parameters on standard and micro tools. Applications range from incoming inspection, in-house regrinding, research, benchmarking, wear analysis, tool setup, in-process control, final inspection to cutting tool certification and reverse engineering. The new »pilot 4.0«operating software equips users to run any measurement and inspection program for any requirement including typical tool measurement of helix angles, radial reliefs, lands, gash angles, head lengths, center offsets, chamfer heights and end face facets to list but a few.
During the IMTS at Booth W432018, connect with any technical experts to get more information or schedule a demo! ZOLLER also has attractive financing options throught our partner LCA availble at the tradeshow!
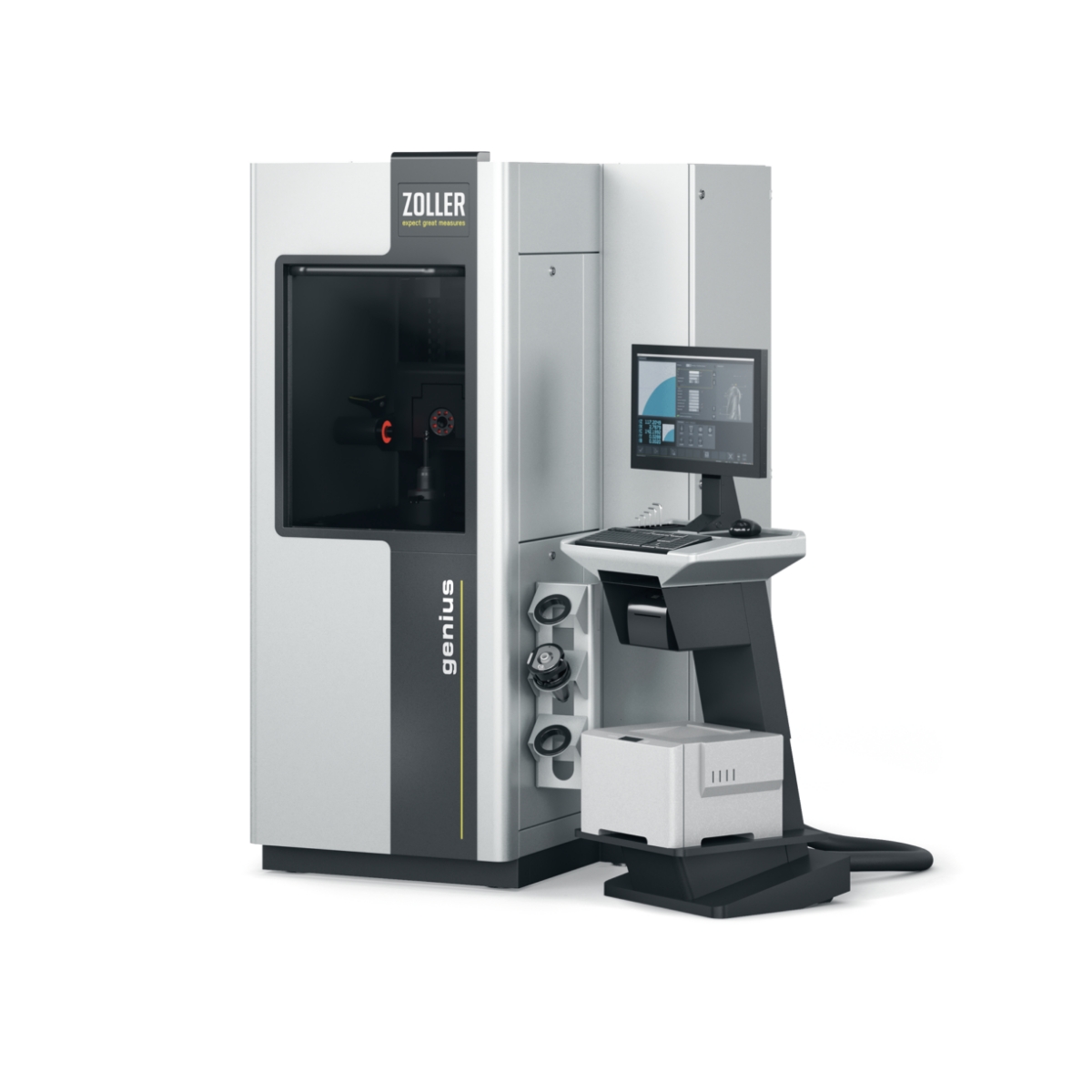
Inspection Solution »genius«
The best selling »genius« is a universal measuring machine and is the perfect solution for the measurement and inspection of your cutting tools quickly, simply and precisely. It can easily handle everything from the quick testing of individual criteria to the fully automatic and operator-independent measurement of more than 100 parameters on standard and micro tools. Applications range from incoming inspection, in-house regrinding, research, benchmarking, wear analysis, tool setup, in-process control, final inspection to cutting tool certification and reverse engineering. The new »pilot 4.0«operating software equips users to run any measurement and inspection program for any requirement including typical tool measurement of helix angles, radial reliefs, lands, gash angles, head lengths, center offsets, chamfer heights and end face facets to list but a few.
During the IMTS at Booth W432018, connect with any technical experts to get more information or schedule a demo! ZOLLER also has attractive financing options throught our partner LCA availble at the tradeshow!
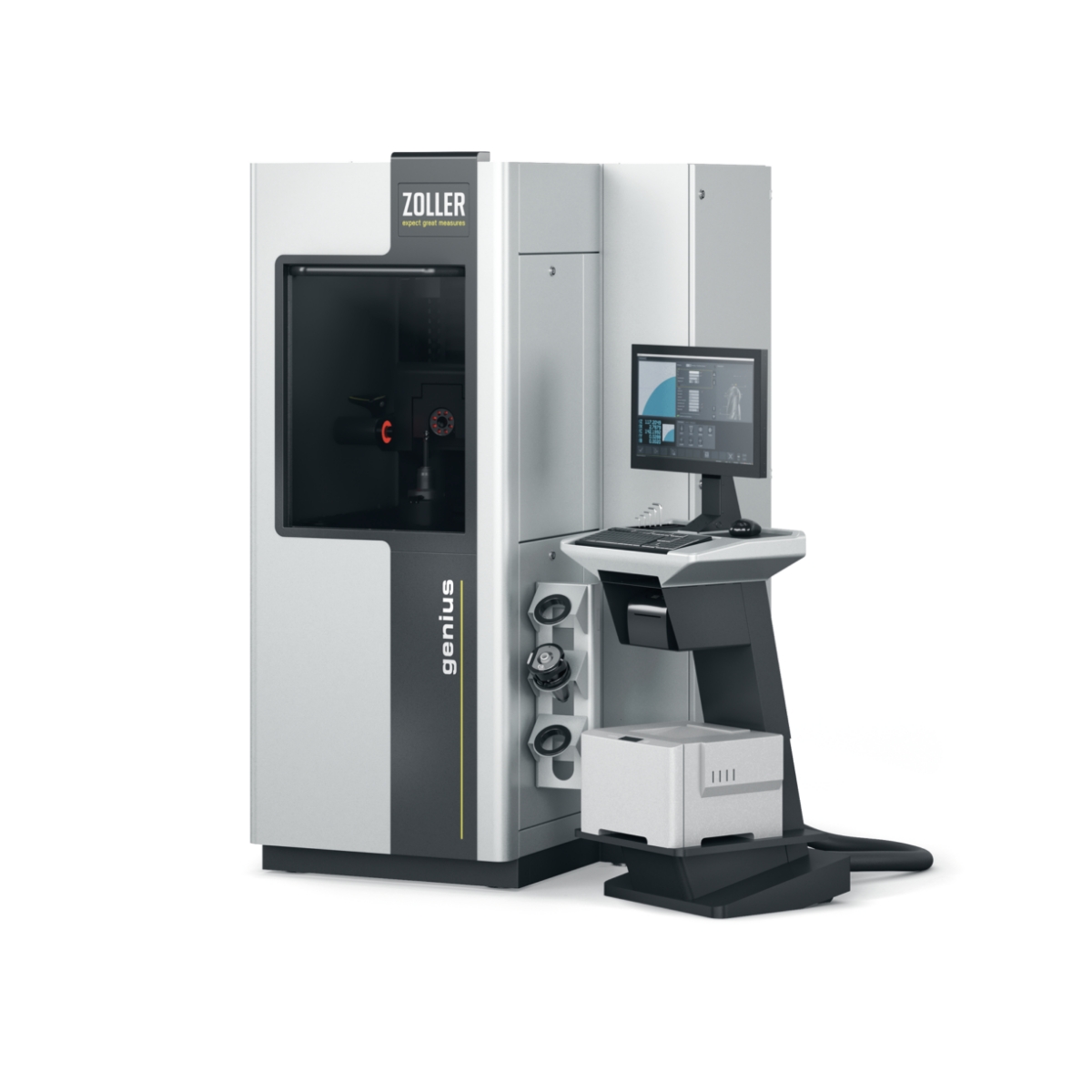
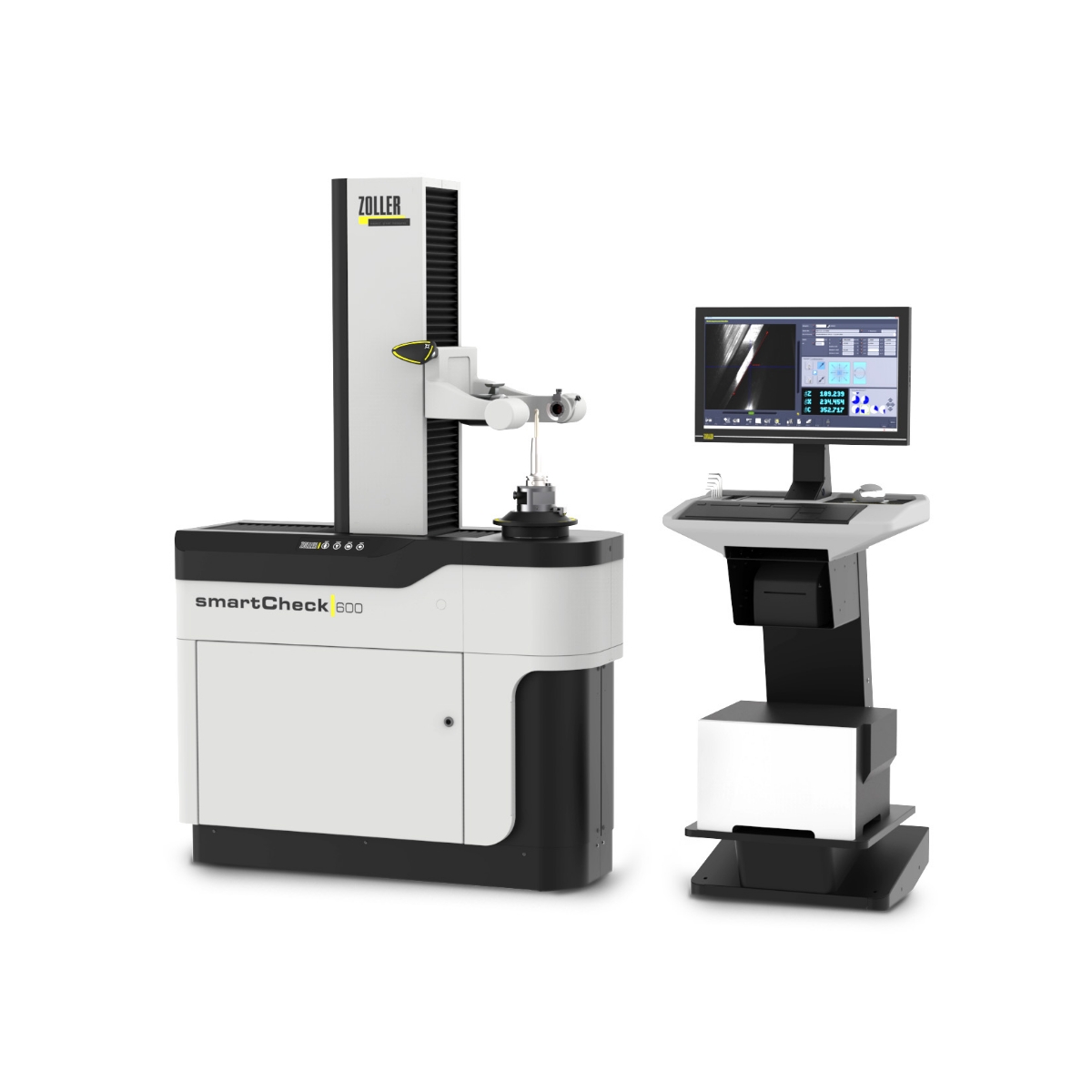
»smartCheck«
Whether as a manual or 3-axis-CNC version: »smartCheck« is the powerful universal measuring machine for all cutting tools! As a result you can check your tools efficiently before and after grinding in order to fulfill DIN EN ISO 9000 guidelines.
In addition, with the swiveling incident light image processing software, you can inspect, measure and document axial and radial geometries of tools — very easily in a single click without expert-level knowledge. You profit directly from at least a 25% productivity increase with your CNC grinding machines simply by measuring your tools before regrinding. Schedule a demo of this gamechanger in tool inspection at the IMTS at Booth W-432018! We look forward to meeting you and showing you this amazing Solution and how it can help you become more competitive, productive and profitable!
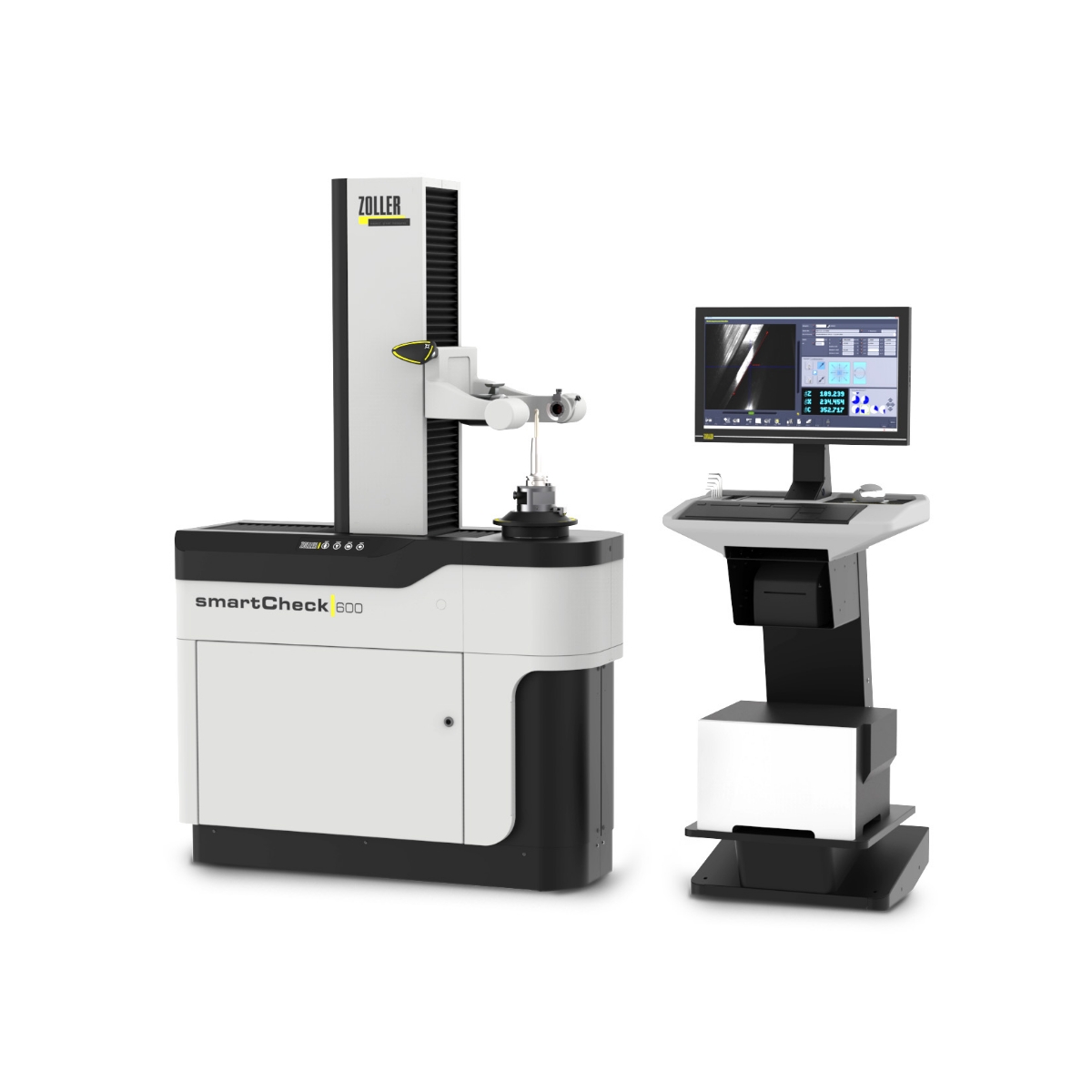
»smartCheck«
Whether as a manual or 3-axis-CNC version: »smartCheck« is the powerful universal measuring machine for all cutting tools! As a result you can check your tools efficiently before and after grinding in order to fulfill DIN EN ISO 9000 guidelines.
In addition, with the swiveling incident light image processing software, you can inspect, measure and document axial and radial geometries of tools — very easily in a single click without expert-level knowledge. You profit directly from at least a 25% productivity increase with your CNC grinding machines simply by measuring your tools before regrinding. Schedule a demo of this gamechanger in tool inspection at the IMTS at Booth W-432018! We look forward to meeting you and showing you this amazing Solution and how it can help you become more competitive, productive and profitable!
»venturion«
Our classic workhorse of the presetting line of Solutions is the »venturion« a presetting and measuring machine that is characterized by unique ergonomics, maximum flexibility and precision. The module design of this presetting and measuring machine gives you the freedom to put together your individual presetting and measuring machine optimally matched to your production processes.
All the basic functions for measuring and presetting your tools are possible with the basic version — you profit from photorealistic input dialogs, automatic cutting edge detection, automatic zero point monitoring and much more. For example, modules can be added for tool inspection, for center height measuring, for measuring reamers or for heat shrinking tools. »venturion« offers every possibility for individual adjustment. Contact us before the IMTS to set up a personalized demo at the IMTS show! We look forward to meeting you!
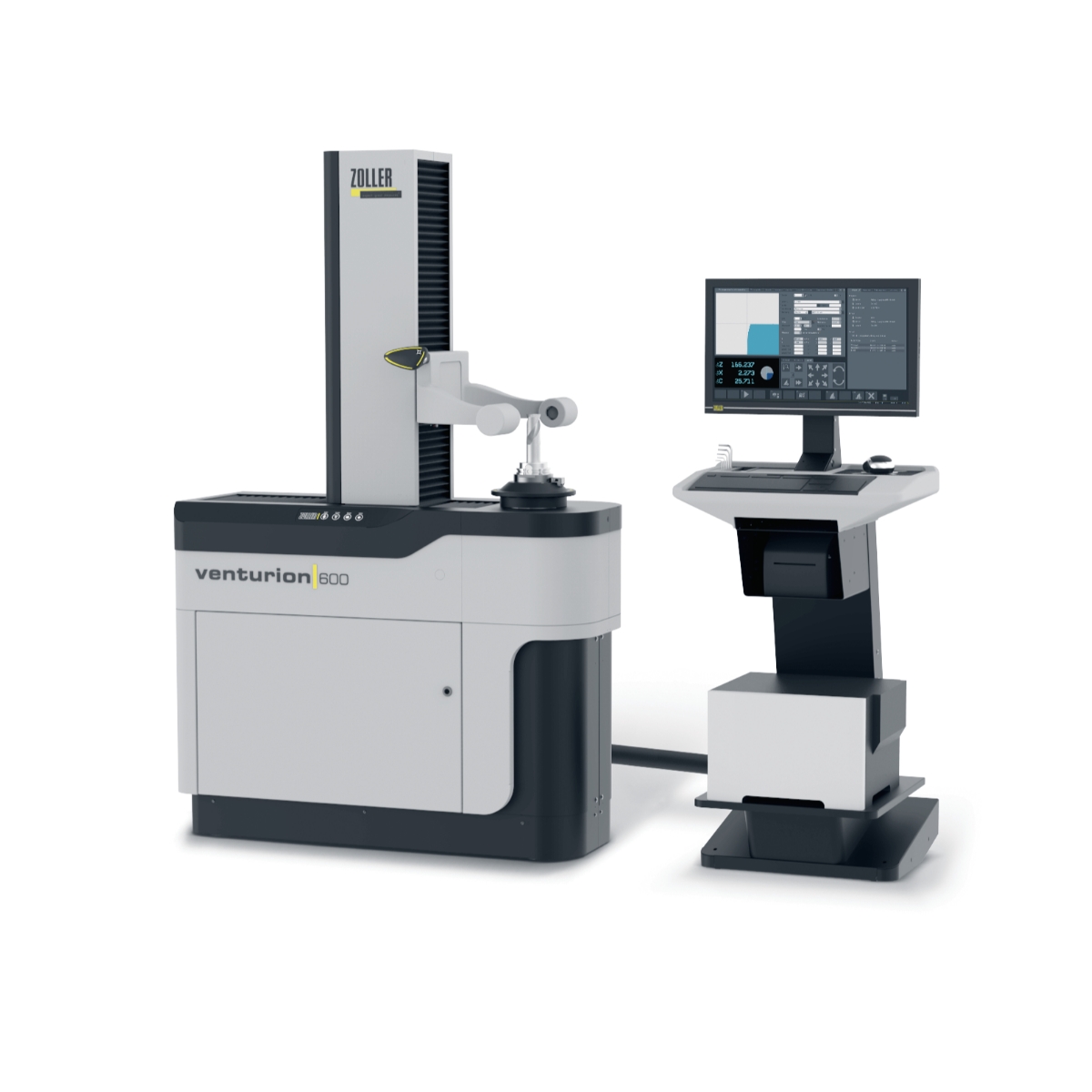
»venturion«
Our classic workhorse of the presetting line of Solutions is the »venturion« a presetting and measuring machine that is characterized by unique ergonomics, maximum flexibility and precision. The module design of this presetting and measuring machine gives you the freedom to put together your individual presetting and measuring machine optimally matched to your production processes.
All the basic functions for measuring and presetting your tools are possible with the basic version — you profit from photorealistic input dialogs, automatic cutting edge detection, automatic zero point monitoring and much more. For example, modules can be added for tool inspection, for center height measuring, for measuring reamers or for heat shrinking tools. »venturion« offers every possibility for individual adjustment. Contact us before the IMTS to set up a personalized demo at the IMTS show! We look forward to meeting you!
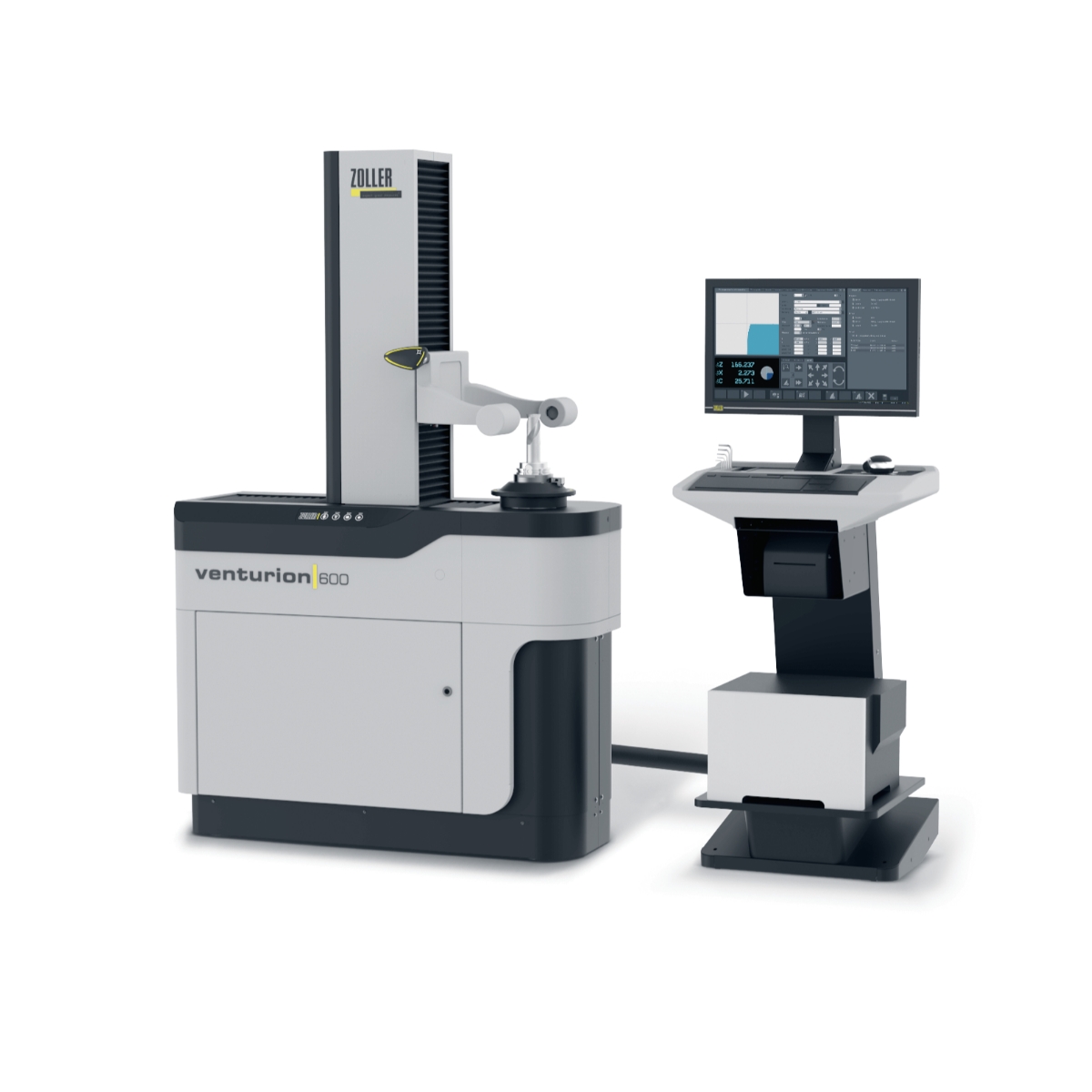
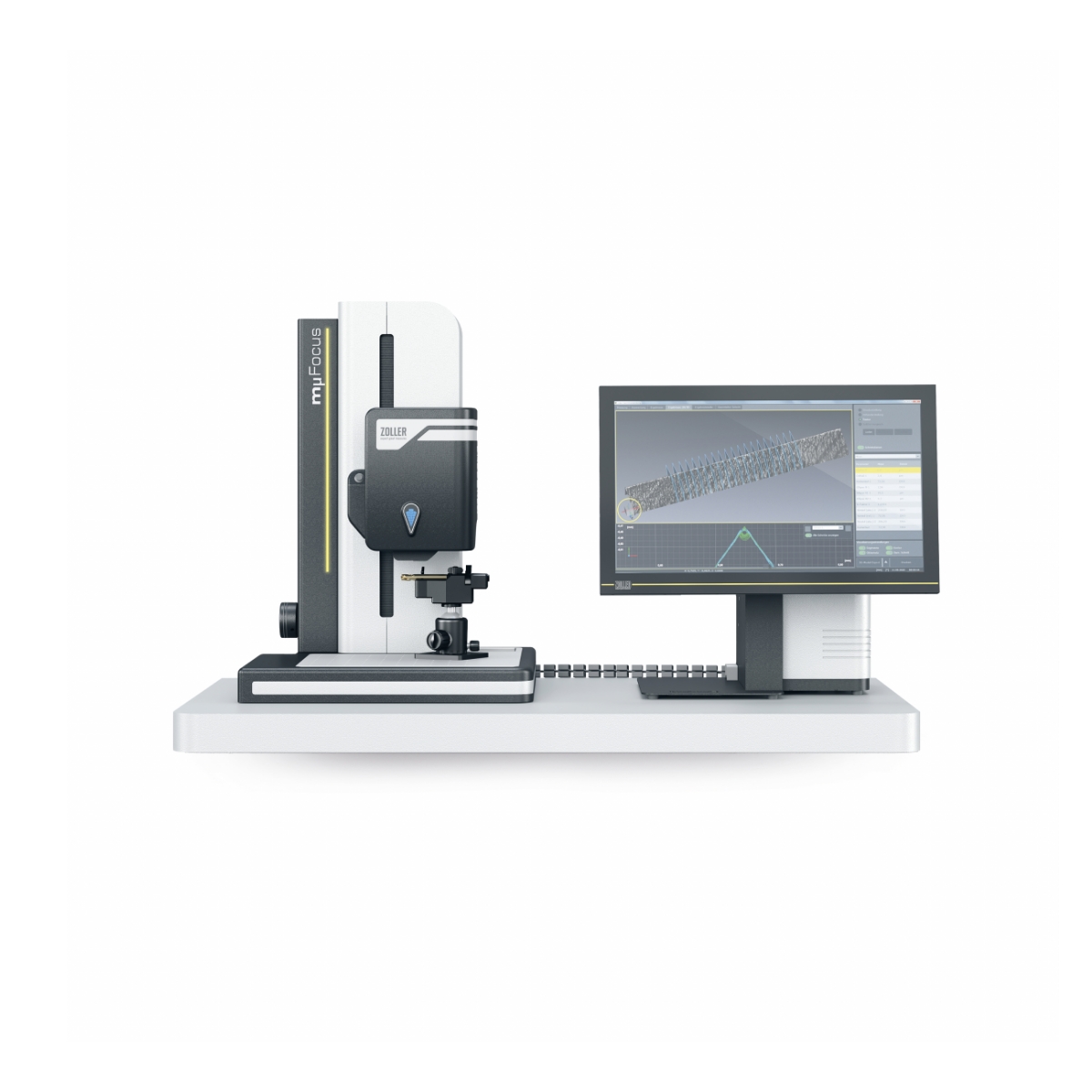
»mμFocus«
You want to produce the perfect cutting edge – one that ensures a long tool life, minimal wear, optimal chip formation, and precision workpiece processing, thereby significantly lowering costs for production.
Achieve your goals with high-precision tool geometry and optimal surface textures customized to your specific application. If you want to ensure exact, standardized quality in your tool development, then the ZOLLER »mμFocus« inspection machine is the right choice for your needs. »mµFocus« uses non-contact measurement procedures to determine the surface roughness and cutting edge prepara-tion of your tool, down to the µm. Use the ZOLLER »mμFocus« to create fully optimized tools.
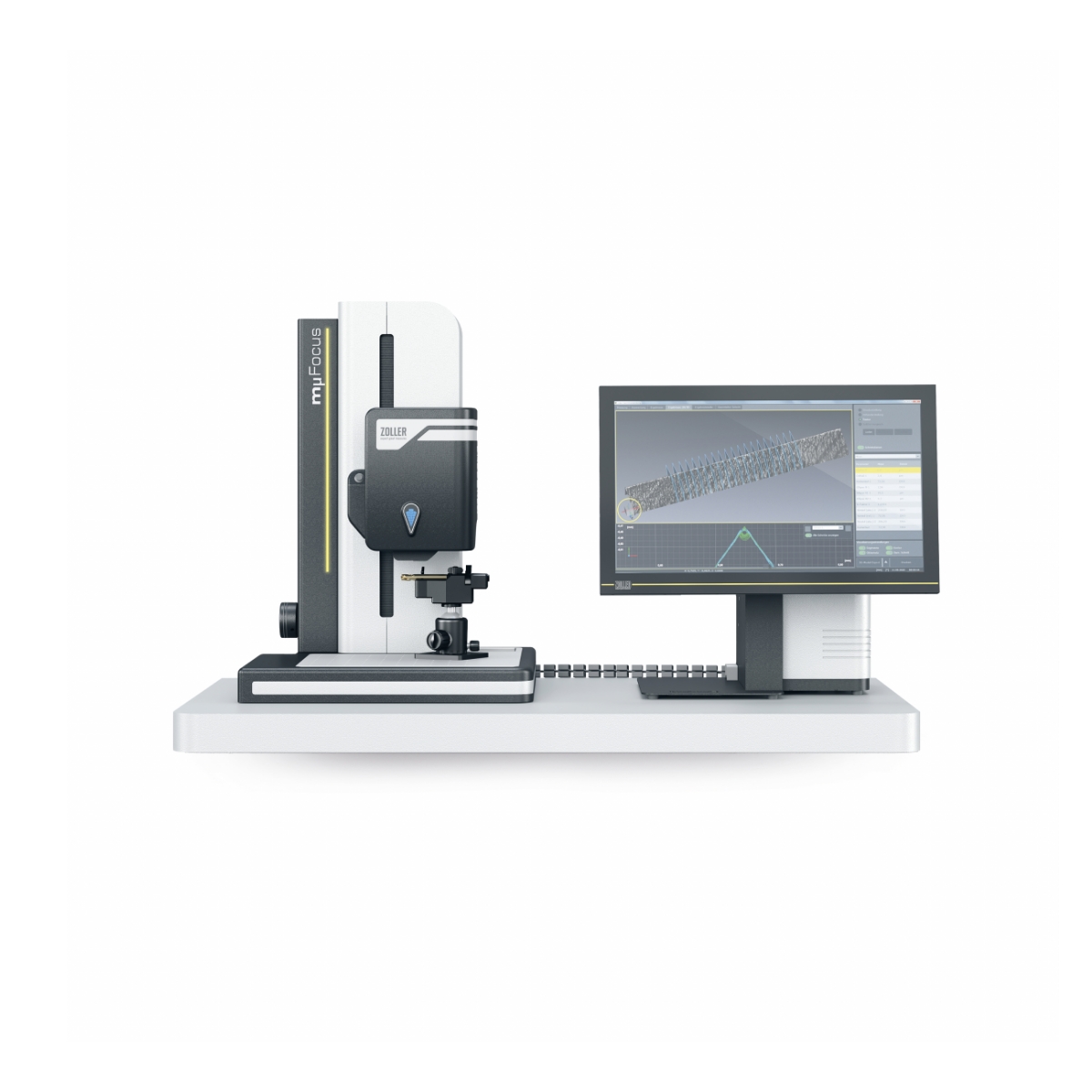
»mμFocus«
You want to produce the perfect cutting edge – one that ensures a long tool life, minimal wear, optimal chip formation, and precision workpiece processing, thereby significantly lowering costs for production.
Achieve your goals with high-precision tool geometry and optimal surface textures customized to your specific application. If you want to ensure exact, standardized quality in your tool development, then the ZOLLER »mμFocus« inspection machine is the right choice for your needs. »mµFocus« uses non-contact measurement procedures to determine the surface roughness and cutting edge prepara-tion of your tool, down to the µm. Use the ZOLLER »mμFocus« to create fully optimized tools.